|
Compressed Air by Bob Adler
For use in bodywork on a vehicle, compressed air has to be clean and dry. After hours of sandblasting, when the compressor runs flat out and gets very hot, air quality plummets and moisture forms, which can contaminate paint work. Here are suggestions for getting the most out of your compressed air without spending a fortune.
How big should my compressor be?
First, forget horsepower. This term used to be equal to 746 watts, or the power necessary to lift 550 pounds one foot in one second. These days, air compressor horsepower is a mythical term that has no relation to how much air a compressor can actually pump. The term that is used to describe output on a compressor is cubic feet per minute (cfm) at a particular pressure, such as 125 pounds per square inch (psi). Find the cfm of the biggest tool you will use, probably a sandblaster, and make sure the compressor can keep up. If you have two workers, better add a factor for that. Remember, a pressure blaster draws more air as the nozzle wears. Plan on buying nozzles one size smaller than the capacity of your compressor, or plan on a compressor a size bigger than required by the nozzles you will use.
 |
Pressure Drop Comparison Chart For Quick Connects The bore on DeVilbiss is much bigger that Milton. (It's also more expensive). |
|
The actual limiting factor may be the size of sand grains that will fit through a nozzle without jamming. Start by purchasing the finest grain sand available. A high-volume, low-pressure (HVLP) spray gun will use about 12 cfm. A pressure sandblaster with a 5/64-inch nozzle lets my 14 cfm compressor cycle on and off (about 10 cfm); when the nozzle is worn to 7/64-inch, my compressor runs continuously, and when it?s worn to 1/8-inch, the compressor can't keep up and lets the pressure at the blaster drop to about 50 psi. This uses lots of sand to do very little cleaning. A small air grinder also uses about 15 cfm.
Compressor manufacturers agree their products have a duty cycle, meaning the pump capacity should be large enough to cycle on and off for a cooling-down period. In reality, we tend to ignore this when blasting. A better quality industrial compressor would tend to last longer under this abuse than a cheap one.
A single-stage compressor sucks in air and pumps it into the storage tank in a single stroke. A single-stage compressor will max out at about 125 psi and is not sufficient for a home-restoration shop. A two-stage compressor uses two cylinders in tandem with an intercooler in between. It is more efficient than a single-stage, giving more air at higher pressure for less energy expended.
Recognize a two-stage compressor by a larger and smaller cylinder connected by a finned pipe, probably wound in a big loop. The maximum pressure that it develops is around 175 psi. Yes, this much pressure is useful for removing stubborn bolts with an impact wrench.
Don't let a two-cylinder, single-stage compressor fool you. A two-stage unit is better. If you don't need 175 psi all the time, the cut in/cut out pressure switch is easy to adjust lower, which saves energy and wear on the motor and pump.
 |
Air Flow-Through HosePressure drops are directly proportional to hose lengths, so if hose length doubles, pressure drop doubles. Use a hose size that gets enough air to the tool. (From DeVilbiss catalog) |
|
Rotary-screw compressors are a completely different type that do not have reciprocating pistons as discussed above. They are more efficient because they do not have a piston constantly accelerating, decelerating, and changing direction, but they do not pump up to pressures higher than about 125 psi. The principle of operation is similar to a gear-type oil pump. I haven't used one.
The compressor tank should be as big as you can find. Eighty gallons is about right. The heat of compression is dissipated in a large tank. Moisture has to condense from a gas to a liquid before a moisture trap can remove it from the air. That's why there is a water drain at the bottom of the tank, and it should be drained frequently. Many compressors are available with a vertical tank, which takes up less floor space than a horizontal layout.
I've been using and abusing an Ingersoll Rand Type 30 model 5N/242 since 1979, with only electric motor and belt replacements. Its output is about 14 cfm at 175 psi, and it has an 80-gallon tank. By 1997, I wanted more air capacity, so I bought another one and now use both. I still use the old one for everyday shop use and set the pressure switch low, to cut out at 140 psi. This is enough air for most of my applications. I figured it takes a lot of electricity to pump up from 140 to 175 psi, so I don't normally go to that high-priced neighborhood. When I do need more pressure or volume, I start the new compressor, which is set to pump up to the full 175 psi. The tank output from the old compressor is plumbed into the new compressor tank, then to my shop tools. This lets heat dissipate through 160 gallons of tank capacity.
I ordered the new compressor with an air-cooled aftercooler. This is a little radiator built into the belt guard that cools the air on its way into the tank. It's a great device and worth getting with a compressor. Many sources I checked were not interested in special ordering a modified compressor. Truman's Inc. and A&I Supply were exceptions. They were happy to quote compressor prices including an aftercooler.
Dry air strategy
When sandblasting for hours, the compressor runs flat out and the tank gets hot. Then moisture does not condense and goes down the hose to contaminate bodywork. It is absolutely necessary to get that moisture cooled, condensed, and removed with a trap before it reaches your tools. For years, I used a second, smaller air tank in series with my original compressor tank. This tank stayed cooler than the first tank but still heated up when sandblasting. My sandblaster came with a moisture trap plumbed into the inlet. A hundred-foot hose further cooled the air. In damp weather I put two moisture traps in the air line.
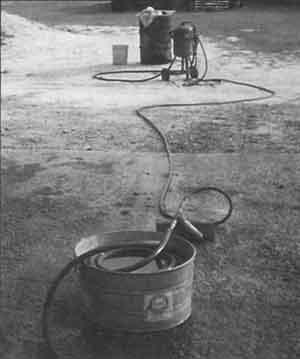 |
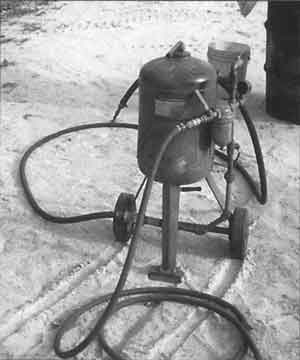 |
Hose coiled in a washtub of water makes a fine moisture condenser. A moisture trap just past the tub is permanently plumbed at the sandblaster. |
|
Years ago, I used to help a friend who had a portable Lindsay gasoline-driven compressor. It pumped lots of air but had a very small tank, which heated up quickly. I bought three 50-foot lengths of half-inch diameter air hose, using two lengths to keep the compressor away from the sandblasting area (upwind so the abrasive did not harm the engine). The third length I coiled up in a washtub full of water for excellent cooling. Cheap and effective!
Pressure losses
There is pressure loss everywhere, and it wastes air and money. Skinny hose and quick connects are the primary culprits. The minimum inside hose diameter should be 5/16-inch for hand air tools. I-IVLP spray-gun manufacturers recommend 3/8-inch hose. For sandblasting I use 1/2-inch nominal size hose, although the actual inside diameter is well over a half inch, closer to three-fourths of an inch.
Like electric wiring, long hose lengths should go up a size in diameter to minimize resistance to flow. Cheap hose gets stiff in cold weather and springs leaks, so don't skimp here. You can use a short length of smaller bore hose at your tools to maintain flexibility if you use a long length of heavier hose to get close. This is also a good place for a moisture trap. I've also heard of cheap hose flaking internally and plugging air tools, but have no experience with this.
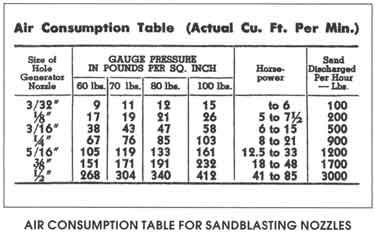 |
All the charts I've seen from hobby-related businesses have low consumptions. This one, from Granite City Tool, St. Cloud, Minnesota, is more realistic. It is an excellent source for sandblasting supplies. |
|
Hose ending and tool quick connects are a necessity, but they do create a pressure drop. I just stuck drill bits down the quick connects to measure the diameter. The typical bore of a 1/4-inch nominal size quick connect is 13/64-inch. I also have some DeVilbiss high-flow quick connects with a 19/64-inch bore. The big connects on my half-inch hose with half-inch pipe threads also have a 19/64-inch bore. If you have a big pressure drop at any location, it will get cold, so feel connectors after a grueling air-tool session. If they are colder than ambient temperature, get higher-capacity connectors. If you have quick connects at places that never get disconnected, plumb the fittings permanently with pipe nipples. They're less restrictive.
Bob Adler is owner of Adler's Antique
Autos, Stephentown, New York, and
specializes in GM truck restoration.
He can be reached at 518-733-5749.
Email
|